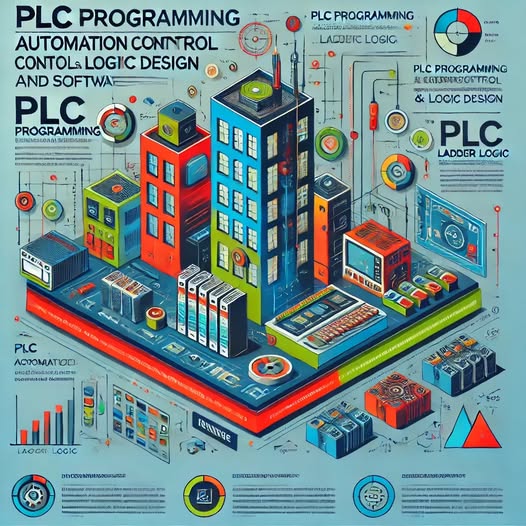
About Course
๐ Course Plan: PLC Programming
Code: 11010-MEP
Title: Programmable Logic Controllers (PLC) Programming for Industrial Automation
๐น Introduction
Programmable Logic Controllers (PLCs) are essential devices in industrial automation, used to control machines and processes. This course introduces participants to the fundamentals of PLCs, their structure, and how to program and integrate them into automated systems.
๐น Description
This course provides a comprehensive overview of PLC systems, from hardware components to software programming. It includes essential programming languages such as Ladder Logic (LD), Function Block Diagram (FBD), and Structured Text (ST). Participants will work on simulations and real-world automation projects using tools like Siemens TIA Portal or Allen-Bradley Studio 5000.
๐น Objectives
-
Understand the structure and operation of PLCs.
-
Learn PLC programming using standard industrial languages.
-
Apply PLCs in the control of industrial equipment and processes.
-
Simulate and debug automation systems.
-
Execute real-life projects in automation and control.
๐น Module 1: Introduction to PLC Systems (6 Hours)
1.1 What is a PLC?
-
Definition, evolution from relay-based systems
-
Role in automation and control systems
1.2 Hardware Architecture
-
CPU, memory, I/O modules, communication ports
-
Power supply and wiring basics
1.3 PLC Types and Selection Criteria
-
Siemens, Allen-Bradley, Schneider, Delta
-
Compact vs. Modular PLCs
-
Industrial application scenarios
1.4 Working Principle
-
The Scan Cycle: Input scan, program execution, output update
-
Real-time processing and cyclic nature
๐น Module 2: PLC Programming Languages (12 Hours)
2.1 Ladder Logic (LD)
-
Basic components: contacts, coils, timers, counters
-
Creating logic diagrams similar to electrical schematics
-
Interlocking, latching, and sequence control
2.2 Function Block Diagram (FBD)
-
Functional blocks: AND, OR, timers, counters
-
Signal flow and modular logic representation
-
Suitable applications in process industries
2.3 Structured Text (ST)
-
Syntax and structure
-
Variables, control structures (IF, CASE, FOR)
-
Advantages in complex logic and arithmetic operations
2.4 Practical Exercises
-
Writing and debugging ladder programs
-
Simulating basic industrial tasks (conveyor, motor start/stop)
-
Converting logic between LD โ FBD โ ST
๐น Module 3: Automation Control Applications (14 Hours)
3.1 Sensors and Actuators Integration
-
Digital vs. analog inputs/outputs
-
Wiring and configuration of proximity sensors, limit switches
-
Output devices: solenoids, contactors, indicator lights
3.2 Real-Life Project Implementation
-
Conveyor belt control
-
Tank level control with sensors and pumps
-
Traffic light automation
-
Elevator logic programming
3.3 Alarm Handling and Fault Detection
-
Signal conditioning and monitoring
-
Generating warnings and logs for faults
3.4 HMI Basics (Optional Extension)
-
Basics of connecting Human Machine Interfaces
-
Displaying status, alarms, and operator input
๐น Module 4: Simulation, Testing, and Debugging (8 Hours)
4.1 PLC Simulation Tools
-
Siemens TIA Portal Simulation
-
Allen-Bradley Emulator
-
General-purpose simulators (e.g., Factory I/O, PLCLogix)
4.2 Debugging Techniques
-
Online monitoring and forcing values
-
Setting breakpoints, watch tables, and diagnostics
4.3 Troubleshooting & Safety Considerations
-
Common programming errors
-
Electrical isolation, short-circuit protection
-
Safe startup and emergency stop design
๐ ๏ธ Software & Hardware Tools
-
Software:
-
Siemens TIA Portal
-
Allen-Bradley Studio 5000
-
Factory I/O or PLCLogix (for simulation)
-
-
Hardware (if available):
-
Siemens S7-1200 / S7-1500
-
Allen-Bradley MicroLogix / CompactLogix
-
Basic HMI panel, push buttons, sensors
-
๐ Course Duration
-
Total Hours: 40 hours
-
20 hours theoretical lectures
-
20 hours practical labs and projects
-
_____________________________________________________
๐น What You Will Learn
-
Basics of PLC architecture and scan cycles.
-
How to program using LD, FBD, and ST.
-
Integration of sensors and actuators.
-
Control of motors, valves, and industrial devices.
-
Troubleshooting and simulation of PLC systems.
-
Real-world project development and implementation.
๐น Target Audience
-
Electrical Engineers and Control Engineers
-
Industrial Automation Technicians
-
Engineering Students (Electrical, Mechatronics, Mechanical)
-
Maintenance and Plant Technicians
-
Anyone seeking foundational skills in automation systems
๐น Materials
-
Personal computer/laptop
-
PLC development software: Siemens TIA Portal or Studio 5000
-
Simulation tools (e.g., Factory I/O, PLCLogix)
-
PLC kits (optional for hands-on labs)
-
Course handouts, exercises, and sample programs
๐น Instruction Methods
-
Interactive lectures and live demonstrations
-
Hands-on practical labs
-
Group discussions and case studies
-
Real project-based learning
-
Continuous practice and guided programming assignments
๐น Time Frame
Total Duration: 40 hours
-
20 hours of theoretical instruction
-
20 hours of hands-on labs and project work
Schedule Options: -
5 weeks (2 sessions per week, 4 hours/session)
-
10-day intensive (4 hours/day)
๐น Course Format
-
Delivery Mode: On-site or Online (Live Virtual Sessions)
-
Content Delivery: Lectures, demonstrations, practical labs
-
Assessment:
-
Weekly quizzes
-
Lab assignments
-
Final project presentation and evaluation
-
๐น Learning Outcomes
Upon successful completion of this course, participants will be able to:
-
Explain how PLCs function in automation systems
-
Develop programs using Ladder Logic, FBD, and Structured Text
-
Connect and control input/output devices
-
Simulate and troubleshoot PLC programs
-
Design and execute a full industrial control project
ย